How the growing use of robots in China will impact different sectors of the economy, as well as the country’s robot makers.
Itʼs a well-depicted scene: a skilled surgeon is performing delicate open-heart surgery in an amphitheatre filled with esteemed colleagues and eager-to-learn residents. The lights illuminating the procedure are bright and hot, calling forth small beads of sweat on the surgeonʼs forehead. The doctor says: “Scalpel.” Only instead of human hands itʼs two robotic arms that extend a tray of tools in response to the surgeonʼs request. No, this is not a summer sci-fi blockbuster, but rather whatʼs happening in Chinaʼs foremost medical research institutions, and in full practice at Beijingʼs General Navy Hospital where robots are the first ones to crack open skulls for brain surgery.
Service robot application in healthcare is only going to increase with time, following the example of Japan and Osaka Universityʼs Actroid-F, a nursing robot with an eerily human appearance. When Osaka University and Kokoro Corporation tested the robotʼs effect on 70 elderly-care patients, only three or four said they didnʼt want it around, with the rest saying that the robotʼs presence was “pleasant”.
“In five years we could have robots working with doctors and nurses,” says Song Xiaogang, Executive Vice-President of the China Industry Machine Federation (CIMF) and President of the China Industry Robot Association (CIRA).
It may be in services that Chinese robotics manufacturers can leapfrog ahead of cutting edge industrial robot technology and establish a foothold in the wider robotics industry.
“It solves the problem of labor costs and lack of labor in some areas. Less and less people would like to do that kind of job,” says Song, citing elderly care as one area where there is less interest in the job market. Furthermore, Chinaʼs leadership is eager to counter the categorical dominance of foreign robotics producers in China, who recently stole the show at the China International Robot Show.
While visitors to the exhibition oohed and aahed over an Italian robot with car assembling capabilities, there was a tense atmosphere behind the scenes during a CEO panel on the Chinese robotics industry Executives ruminated on the implications of Chinaʼs newly minted status as the worldʼs largest robotics market. Stefan Sack, CEO of Italian firm Comau Engineering, warned against letting small robot manufacturers pop up “like mushrooms”, further fragmenting a market in need of improved integration and downstream supply chains. He warned fledgling domestic industry players: “Everyone wants to become a robot manufacturer because it sounds sexy. It will not be sexy.”
In 2013, China purchased one in five robots sold globally—a total of 36,560 units—unseating Japan as the worldʼs largest buyer of robots according to the Germany-based International Federation of Robotics (IFR). Rapid automation of manufacturing and services highlights opportunities for both Chinese and foreign robotics companies.
But China still lags far behind more developed countries both in the production and use of robotics. The country has only 11 robots installed per 10,000 manufacturing employees, in contrast to South Korea, which has 396.
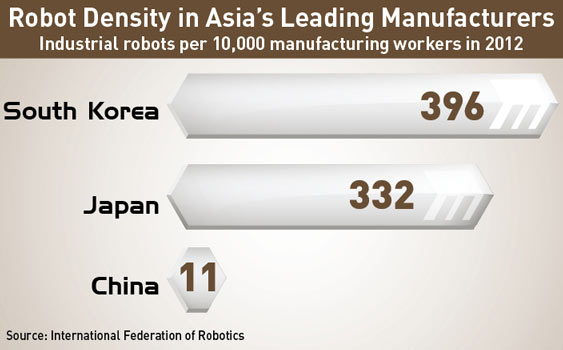
2, 4, 6, 8 Everybody Automate!
Chinaʼs status as the fastest-growing market for industrial robotics means that relatively virgin robot territory could be set for some serious growth.
Robot sales grew 36% on average per year from 2008 to 2013, according to the IFR report, with the auto sector retaining its role as the main driver of the automation boom with 60% of all auto production depending on robotics. Liu Jianshuo, Sales Manager at Beijing RHJ Robotics Technology, says automobile manufacturers are his companyʼs biggest customers, with welding robots leading the charge.
But packing robots are also holding their own. Liu Yang, Sales Manager at Swiss mechatronics company Stubliʼs Hangzhou office: “Pallet packing robots in the food packaging industry and electronic assembly industry are selling best.”
As for the future of the automation boom, cars will have their place for at least several more years to come. Market research firm Transparency Market Research forecasted in 2013 that major growth would be seen in pharmaceutical production as robots are increasingly used for washing, labeling, packaging and other end-process tasks.
There are a number of reasons that companies are incorporating robots at ever greater adoption rates.
“When you introduce automation in robotics, it commands, it requires, it will dictate a sort of improvement of the whole process,” says Arturo Baroncelli, IFR President.
Simply put, robots improve efficiency. “2013 was a very, very strong year for robotics, which is interesting because it wasnʼt a great year for a lot of other machines like machine tools. So I take that as a sign that China is automating, even though theyʼre not automating to increase capacity, theyʼre automating to improve efficiency,” says Morten Paulsen, Head of Japan research at CLSA. Were capacity the aim, we wouldnʼt see such a gap between machine tools and robots, he adds.
Furthermore, when put to certain tasks where robotics can guarantee a level of precision and safety that humans canʼt, robots increase productivity. Swiss power and automation technology company ABB released reports going as far back as 2010 detailing how the use of robots in welding increased productivity by 60%.
But in the macro-economic sense, firms adopt robotics in manufacturing to save on the costs of labor wages, which have risen rapidly in China. In fact, there are several aspects of Chinaʼs workforce that necessitate a serious evaluation of what part of production can be automated.
A Losing Wager
Chinaʼs workforce shrank for the first time in 2012 with the working-age population falling by 2.4 million people to 920 million by 2013. State media reported in February this year that labor supply has fallen to half of demand in Beijing. According to local government agencies, the city will have only 218,000 people available against 556,000 new positions that will open up in the first six months of this year. China may be arriving at what is known as the “Lewis turning point”, whereby a country runs out of surplus labor, driving wages up.
One company that has been hit hard by rising wages is Foxconn Technology, the Taiwanese manufacturer of Appleʼs iPhones and iPads, best epitomized by its city-sized factory complex in Shenzhen. Foxconn saw its labor costs rise by 16.5% in 2009, by 25% in 2012, and promised to double wages again in 2013, though whether or not that hike has taken place has yet to be confirmed. What has taken place is a steady increase in the minimum wage in Shenzhen, which already has the highest minimum wage requirements in China. At the very end of 2013, Shenzhenʼs Mayor Xu Qin announced that the hourly minimum wage requirement would go up 13.5% to RMB 16.5 an hour. Thus the same cost pressures that are prompting companies to evaluate other manufacturing locations such as Southeast Asia are also pushing companies to automate.
Foxconn, for instance, is building an army of robots to supplant an ever-more expensive human workforce. Itʼs hard to know how many robots Foxconn has and how sophisticated they are, because the companyʼs “Foxbots” are made and used exclusively in-house. However, ABB told analysts at CLSA that Foxconn may be producing more robots than the rest of the Chinese industry players combined.
Feeding the Machine The New Factory Floor
The global industry for factory robotics is largely dominated by four firms—Fanuc (Japan), ABB (Switzerland), Yaskawa (Japan), and Kuka (Germany)—which provide two-thirds of global supply. The dominance of Japanese and Western firms is mirrored in China, where foreign providers control some 90% of the market according to IFR data.
That dominance appears likely to continue for some time. Paulsen argues that three factors are holding Chinese robotmakers back, preventing them from posing a serious challenge to foreign providers, at least for now. The first is technology: “Thereʼs a pretty significant gap,” says Paulsen, between Chinese and foreign-produced robots and automation equipment in terms of speed and precision.
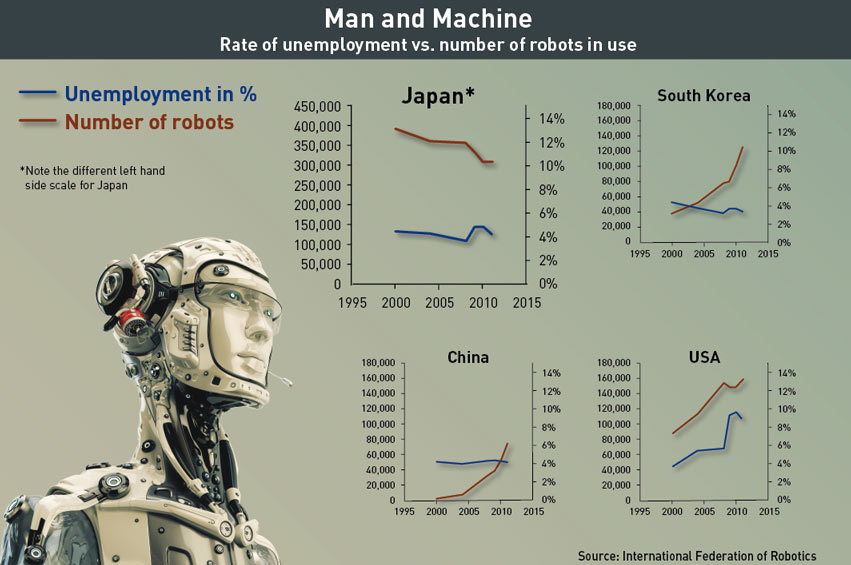
Another challenge is that many of the key components of domestically-made robots are imported. Sophisticated parts like servo motors, controllers and software are mostly bought from Europe and Japan. “Whatʼs left of the robot is basically the iron casting and the assembly,” says Paulsen. “So itʼs a robot thatʼs made in China but without in-house production of key components; it will be difficult for these companies to gain a real price advantage and technological edge compared to foreign competitors.”
Branding represents a third roadblock for Chinese firms. Customers, including both Chinese and foreign partners in joint ventures, are reluctant to stray from the big four global providers with their long histories and well-established brands. But that may change over the next five to 10 years, with Chinese robotics firms like Guangzhou-based GSK, Wuhan Huazhong, and Beijing CND emerging as potential domestic leaders.
Paulsen predicts that one or two of these companies will eventually take their place among the big four global robotmakers in China. These companies are well-managed, forward-thinking, and profitable, he argues. They also enjoy a high degree of state subsidies and support via robotics research institutes.
Chinaʼs leading domestic provider of industrial robots is privately-owned GSK. GSKʼs management claims the company accounts for 30% of the Computer Numerical Control (CNC) machine tool units produced in China. But the countryʼs leader in CNC systems may in fact be Wuhan Huazhong. Founded by a group of state-owned enterprises and private venture capitalists, the company claims a 66% share in the high-end and a 30% share in the mid-end domestic CNC markets. Overall, even this market as a whole is dominated by Fanuc and Germanyʼs Siemens.
If the supplier landscape is changing, so is the nature of robot work. Traditionally, robots have been employed mainly in the automotive and electronics manufacturing sectors in China.
The automotive sector, which is dominated by large multinationals, accounts for 60% of current demand. But Song sees huge potential growth in robot use in a wide range of manufacturing industries: food processing, chemicals, home appliances, and construction materials, among others.
“Itʼs very vast sectors of manufacturing,” Song says. Already, 25 of the 36 manufacturing sectors identified by the government use Chinese robotics in production. Song said he believes that virtually all production can be robotized, quipping that marketing and R&D are the only sectors truly immune to automation.
The New Factory Floor
Anxiety over job security as it relates to automation is propelled primarily by the workers. Neelie Kroes, Vice-President of the European Commission, even demanded that robot makers reassure the public that their machines will not usher in a dystopian, jobless economy when launching a robotics research fund in June of this year.
Various advocates, however, discount that scenario, claiming that automation actually creates new jobs that are more productive, more interesting and better-paid than the jobs that robots destroy. Robot application comes with its own labor demand, such as in their design, programming, operation and maintenance.
Instead of replacing humans entirely, except where there are tremendous safety benefits, robots will increasingly be seen working alongside humans on assembly lines. In more developed economies, “collaborative robots,” or “co-bots”, those that work alongside workers, are changing the nature of factory work. The co-bots take on the dullest and most repetitive tasks, freeing their human counterparts up to focus on more interesting and creative work. Such collaborations will ultimately raise Chinaʼs manufacturing game, not degrade it. No matter how efficient manufacturing in the US becomes, nowhere else in the world can compete with Chinaʼs infrastructure or manufacturing ecosystem.
But robot-human collaboration calls for some risk management that companies will have to deal with. Weng Yueh-Hsuan, a research associate at Peking University Law School, argues that the development of man-machine collaboration calls for more regulation. “From a risk regulation perspective, I believe we will need a legal framework to deal with the new machine safety for human-robot co-existence,” Weng says. “I think a sound domestic labor policy guideline will be necessary to China, in order to ease the tension relationship between robot and human workers.”
Chinaʼs factories can only benefit from more robotics adoption and better application, and what weʼve seen so far is that jobs are rather enriched by automation.
“I think there are other dynamics at work in China. Itʼs to get a different cost curve, get better economies of scale and improve quality. Those would be the main drivers,” says Paulsen. “Manufacturers are putting more capacity in China than theyʼre taking out on the net level.” Robot adoption can help China solidify its status as a top manufacturing destination. As Baroncelli repeats, this is the way manufacturing is going regardless, so China best be on board.
“Itʼs not a question of using or not using robots,” he says. “In a growing economy, you must do things with robots. End of the story.”